Fast and Flawless Rewinding
The Danish Solar Group has almost everything in its product range needed by construction and trade companies - including a large selection of cables and wires. In order to provide these to customers in the quantities they require, the company relies on winding technology from KABELMAT in its logistics centre in Vejen: three fully automatic AUTOLOG winding systems and several individual machines ensure efficient and gentle handling - even of sensitive optical fibres.
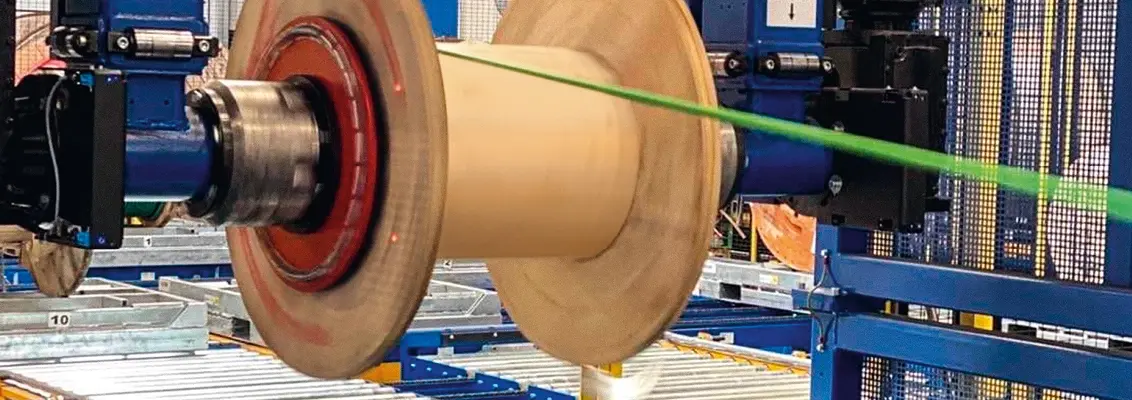
From screws to generators, from lamps to photovoltaic systems, from bathroom fittings to smart home systems: the Danish Solar Group's product range offers construction and trade companies everything they need to realise their projects. Established in 1919, the company is specialised in procurement as well as services related to electrical, heating and sanitary engineering, ventilation as well as air conditioning and energy solutions - and is extremely successful in these areas. The Solar Group is not only active in Denmark, but also in Norway, Sweden, the Netherlands and Poland. In 2021, the company achieved a turnover of almost 12.4 billion Danish Kronen (1.67 billion Euros) with 2,900 employees.
Tailor-made cables based on customer requirements
In addition to a modern logistics concept and excellent service, an extensive product range and high product availability are major strengths of the Solar Group. Their portfolio also includes a huge selection of cables and wires: from control and connection cables for industry and mechanical engineering, to cables for infrastructure and building technology, to fibre optic cables, telecommunications and data cables, no wish remains unfulfilled. "It is our ambition to make our customers' processes more efficient and sustainable," explains Kim Søllingvraa Nielsen, Team Leader Cables, Volume & Long Goods. "That's why we also supply cables and wires not only in standard lengths, but also tailored to customer requirements."
To this end, the company is also well prepared from a technical perspective: in its 45,000 square metre logistics centre in Vejen, Denmark, Solar has, among other machinery, three automatic wrapping lines. These machines unwind cables and wires from the manufacturers' and suppliers' large drums, which weigh several tonnes, and wind them onto smaller drums or into coils for boxes - precisely cut to the length ordered. "Considering the number of orders we handle, this process would be impossible to do manually," Nielsen explains.
These systems were supplied and installed by HELUKABEL’s subsidiary KABELMAT Wickeltechnik. "We used another supplier's machines until recently," Nielsen remembers. "However, they were getting old and no longer achieved the desired results in terms of quality and productivity." After visiting several manufacturers, those responsible at Solar finally decided on the AUTOLOG rewinding machines from KABELMAT.
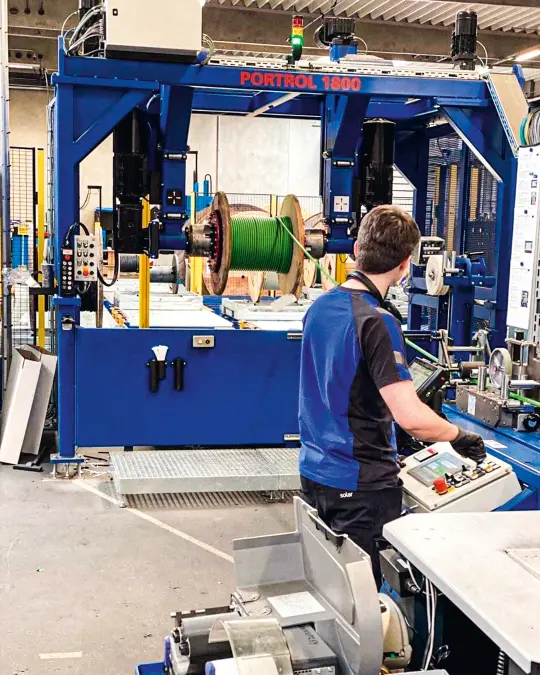
OTHER POSTS >>> PLASTIC DRAG CHAINS, ARE THEY REALLY GOOD?
Automatic control avoids operating errors
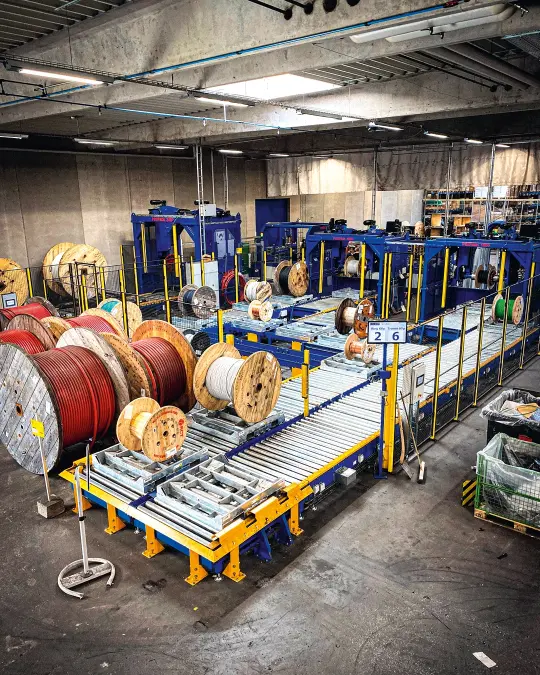
The systems are made of several machines, each with a modular construction and available in different sizes: three PORTROL drum unwinders pick up the drum to be unwound with a quill and bring it into position. They are connected to a conveyor line, and so a drum can automatically be retrieved from the warehouse and transported to the drum unwinders. On the opposite side, two UMROL rewinders and a semi-automatic cable coiling machine from the RINGROL series wind the cables onto drums of different sizes and into boxes, while simultaneously measuring the correct length and cutting them to order. The unwinding and rewinding are controlled automatically, the system receives the order data via an interface to the ERP system. "This eliminates operating errors," emphasises Nielsen. Finally, the completed rolls and boxes only need to be removed with the forklift truck and prepared for shipping. "This saves a lot of time and manpower."
One particular challenge at Solar Danmark was the cutting of high-quality glass fibre cables: these should not be bent too much when being wound in order to avoid damage. "Therefore, we specially adapted the bending on the systems to ensure that no bending radii are too tight," explains Manfred Wössner, Sales Manager at KABELMAT. A so-called cable dancer system, which is positioned between the unwinder and rewinder, also compensates for speed fluctuations and thus reduces the tensile load on the cable. "This allows even sensitive products such as optical fibres to be cut to length and wound without any quality loss," adds Wössner.
Highest quality and maximum availability
In addition to the three fully automatic lines, Solar Danmark also uses three UMROL 1000 rewinders. On these more compact machines, the company can wind cables and wires into coils or onto smaller drums without having to use one of the rewinding lines - for orders with small batch sizes, for example. All KABELMAT machines are calibrated in accordance with the European Measuring Instruments Directive (MID) and are thus approved for use throughout Europe. Furthermore, they are equipped with data storage devices that allow all work steps to be traced back without any gaps. "All this ensures that we can offer our customers the highest quality and maximum availability," says team leader Nielsen happily. "It has been possible to significantly increase our throughput with the new equipment."
Another advantage is the user-friendliness of the KABELMAT machines: they are equipped with high-quality Siemens touch panels and have a Danish voice output - consequently, the changeover was a piece of cake for the staff. "We also received in-depth training from KABELMAT after commissioning, so no questions were left unanswered," says Nielsen, praising the cooperation. "We are completely satisfied with our new winding technology, and another machine is already being planned to further expand our capacity here."
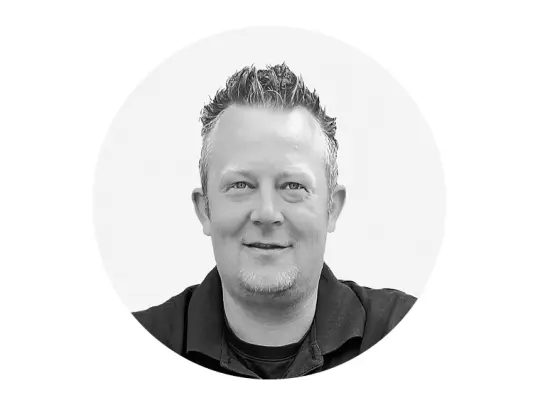
OTHER POSTS >>> UP IN THE AIR WITH VINPEARL SKY WHEEL