What are aluminum cables? Their features and applications
Aluminum cables are lightweight and ideal for applications where space is not a limitation. Discover the key features and advantages of aluminum cables in this article.
Choosing the right electrical cable for each industry and specific application can be challenging. Copper is commonly used thanks to its excellent conductivity and flexibility. However, copper is heavier and more expensive than aluminum.
In many cases, aluminum cables are a practical alternative due to their significantly lighter weight and lower cost. Still, to use aluminum effectively, it's important to understand its electrical characteristics and how to overcome its technical challenges.
1. What are aluminum cables?
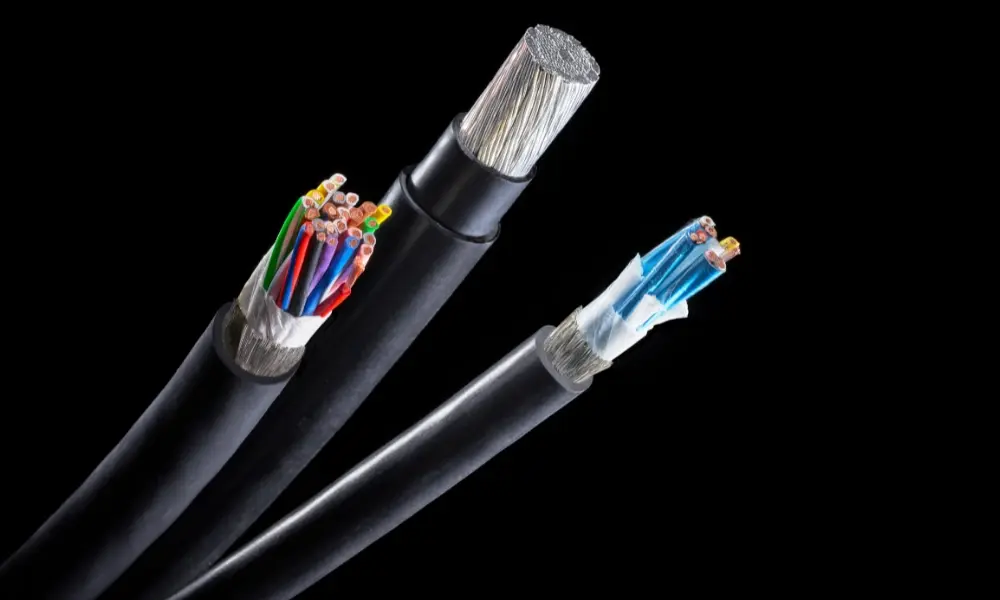
Aluminum cable is a type of cable with an aluminum conductor core used for power transmission. Aluminum is a good electrical conductor, lighter than copper, and more cost-effective, making it widely used in medium- and high-voltage transmission systems, especially in energy and electrical infrastructure sectors.
Typical components of an aluminum cable include:
- A conductor made of pure aluminum (Al) or aluminum alloy, with a cross-sectional area suitable for the required current load.
- An insulation layer (such as XLPE or PVC) covering the conductor to ensure electrical safety and prevent leakage.
- An outer sheath (for sheathed cables), providing resistance against environmental, mechanical, or chemical effects.
2. Common misconceptions about aluminum cables
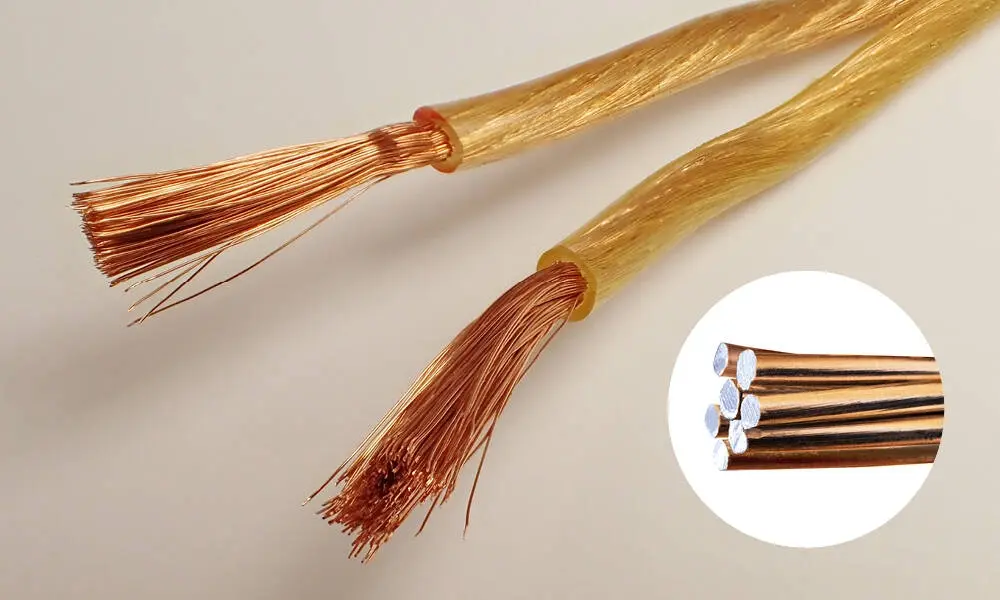
Although aluminum cables have been used safely and effectively in the electrical industry for decades, several misconceptions still create hesitancy among consumers and some investors. Here are the most common misunderstandings and the truths behind them:
2.1 Misconception 1: Aluminum is phased out of many electrical devices due to incompatibility
Some manufacturers have discontinued the use of aluminum conductors in certain products, which is often misunderstood as proof that aluminum is unfit for electrical applications. In reality, this choice is usually due to design standards, product optimization, or business strategy—not because aluminum is low-quality or unsafe.
2.2 Misconception 2: Aluminum is a poor conductor due to its higher resistance
Aluminum has about 60% higher resistivity than copper, meaning a larger cross-section is required to carry the same current. However, when properly engineered - with the right conductor size and compliant connections - aluminum cables can still ensure safe and efficient conductivity, especially in industrial and power transmission applications.
2.3 Misconception 3: Lower price means lower quality
Aluminum’s lower price is due to its abundance and easier processing - not because it's technically inferior. With corrosion resistance, lightweight properties, and good performance, aluminum cables are reliable for industrial, residential, and renewable energy applications.
3. Outstanding characteristics of aluminum cables
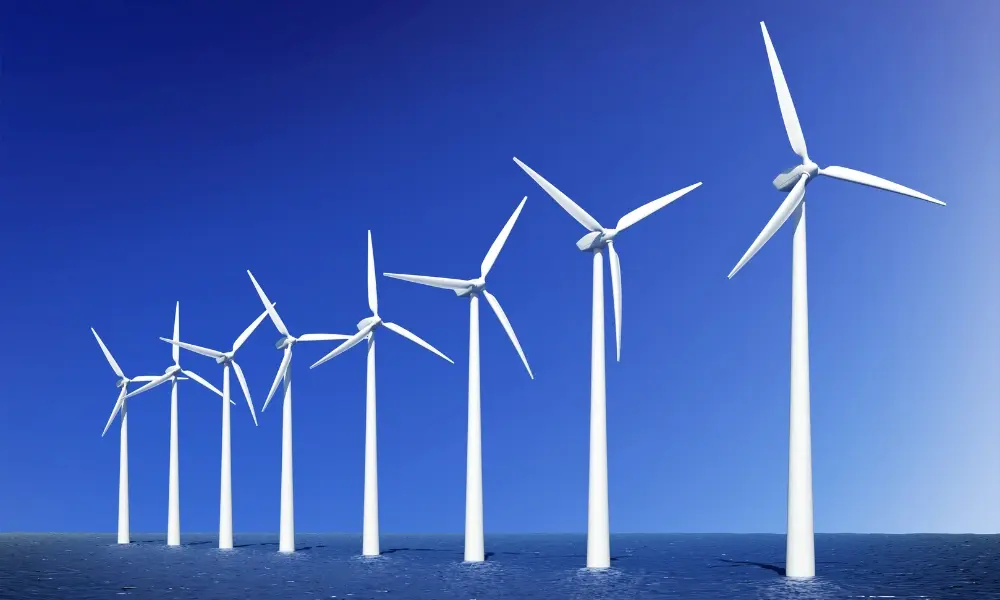
3.1 Lightweight yet durable
Aluminum is up to 70% lighter than copper, offering:
- Easier installation and reduced load on cable trays and support systems
- Less tension on overhead transmission lines
- Optimized weight in mobile systems like cars, aircraft, and wind turbines
Example: The Airbus A380 uses all-aluminum wiring harnesses to reduce total weight.
3.2 Natural corrosion resistance
Like copper, aluminum oxidizes when exposed to air. However, aluminum forms a thin, hard, and transparent oxide layer that protects it from further corrosion. This makes it highly durable in outdoor, coastal, or mildly chemical environments.
Copper, on the other hand, continues oxidizing over time, which may affect joint conductivity if not properly treated.
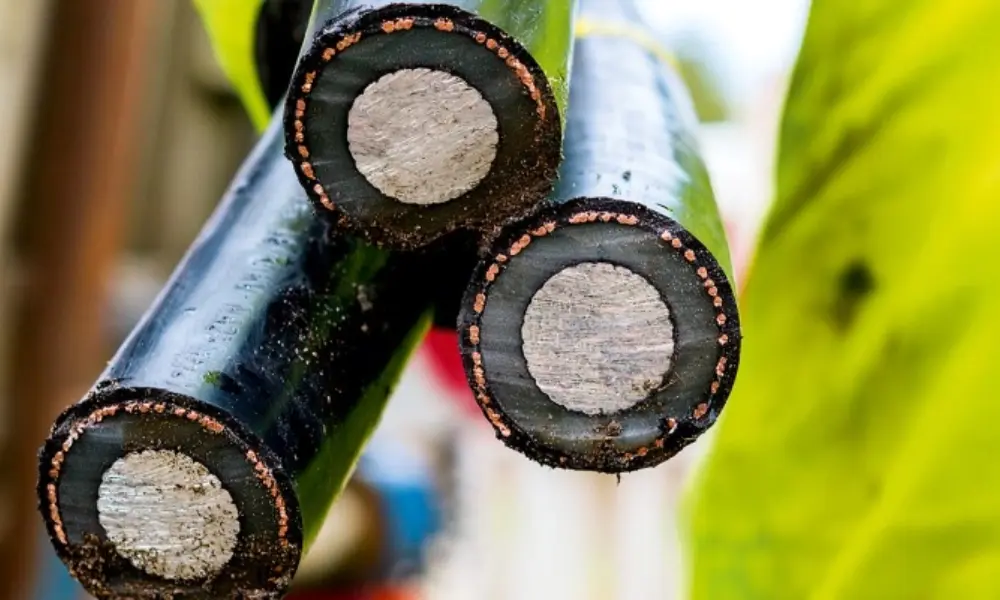
3.3 Larger cross-section, same performance
Since aluminum has lower electrical conductivity than copper, aluminum cables need to have a cross-sectional area approximately one-third larger to carry the same current. However, when combined with suitable insulation materials, aluminum cables can still deliver performance equivalent to standard copper cables.
To achieve the same current-carrying capacity, aluminum conductors must be larger in size than their copper counterparts. This is not necessarily a disadvantage, because:
- A larger conductor surface area enhances the utilization of the skin effect in alternating current (AC) systems - where current tends to flow near the surface of the conductor—resulting in more efficient conductivity.
- A larger cross-section also provides greater contact area at joints, which reduces current density at the contact point, lowers heat generation, and extends the lifespan of the connection.
If the electrical system allows sufficient space for installing larger aluminum cables, this becomes a clear advantage in both performance and cost. The only limitation of the larger size arises in confined spaces, such as inside control cabinets with high component density. Outside of such situations, the increased size is generally not a significant obstacle.
3.4 Aluminum offers efficient electrical and thermal conductivity
Aluminum is an excellent conductor of both electricity and heat - second only to copper. Its thermal storage capacity is 0.214 cal/gram/°C, which is 2.3 times higher than that of copper (0.092 cal/gram/°C). This means:
- Aluminum cables can absorb and dissipate heat more effectively.
- They can withstand current surges and overloads without being damaged.
This is why, in many devices such as transformers, aluminum windings often handle overload currents better than copper windings.
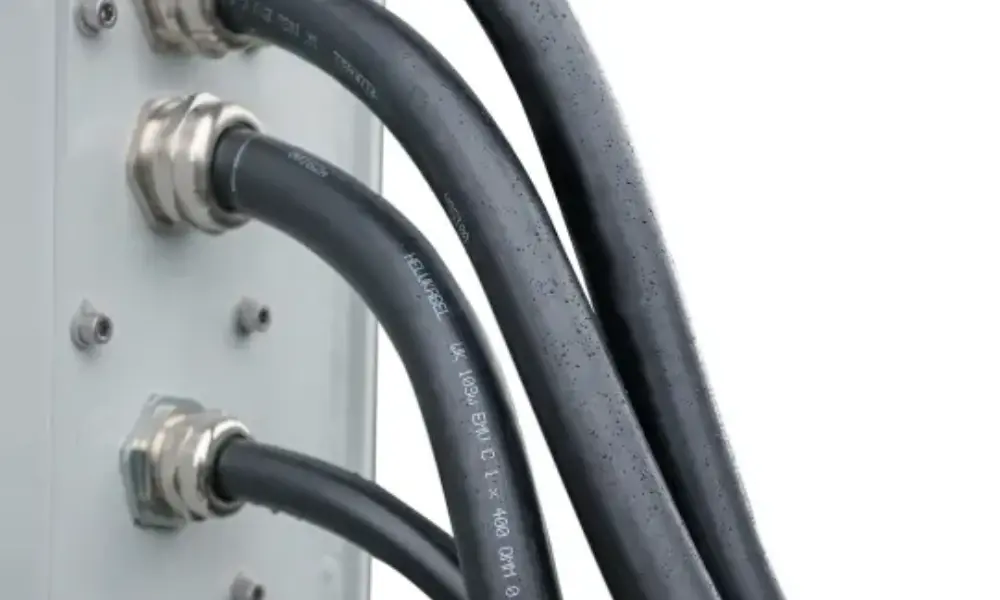
3.5 Easy to bend and highly flexible
Aluminum is highly ductile, making it easy to fabricate, bend, roll, or form into complex shapes without cracking. In the past, aluminum cables were not typically used in flexible wiring applications. However, this has changed with modern solutions like HELUWIND® WK POWERLINE ALU from HELUKABEL, which uses fine-stranded aluminum conductors combined with specialized terminals - enabling aluminum to be used flexibly in high-mechanical-strength applications.
3.6 Aluminum cables are recyclable
Aluminum is a fully recyclable material, and importantly, it retains its physical and chemical properties through the recycling process. This helps to reduce industrial waste, conserve natural resources, and lower greenhouse gas emissions during production.
3.7 Aluminum cable costs less than copper cables
As global metal prices continue to rise - especially for copper - many industrial companies are re-evaluating their material choices to reduce investment costs and optimize system weight.
Aluminum has become a practical alternative due to its significantly lower price and much lighter weight compared to copper.
4. Applications of aluminum cables
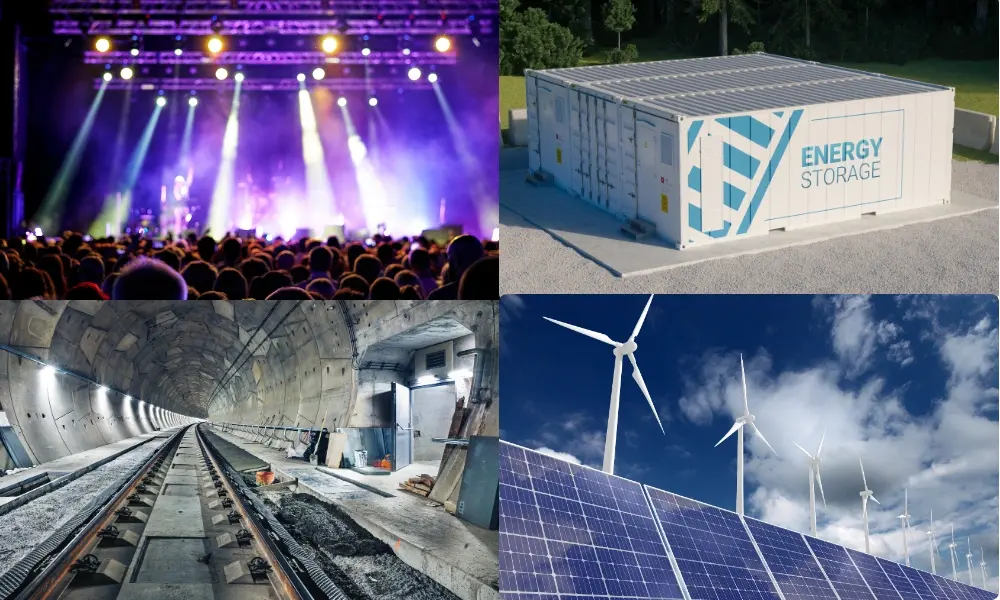
With the right technical properties, aluminum cables are becoming an optimal solution for many modern electrical systems - from renewable energy to heavy industrial projects. Key application areas include:
- Railway industry
- Telecommunication technology
- Combined heat and power systems: internal power distribution and thermal-electric device connections
- Photovoltaic (PV) solar power systems
- Wind power systems: connecting wind turbines to substations and transmitting electricity from offshore turbines
- Industrial construction: power plants, substations, and industrial facility infrastructure
- Energy storage systems
5. HELUKABEL’s aluminum cables
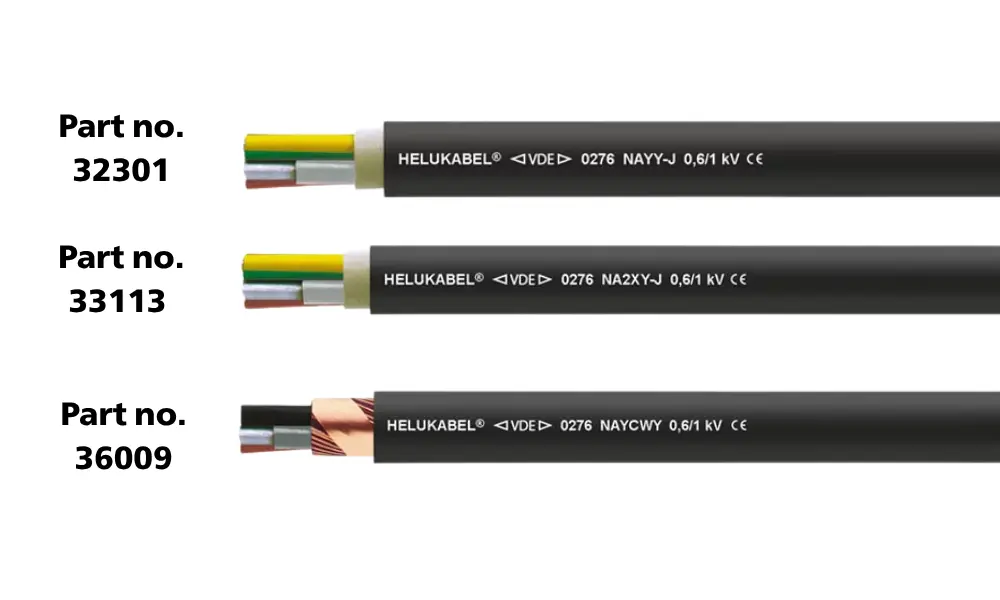
5.1 RE/SE/SM 0,6/1KV aluminum cables
The abbreviations RE/SE/SM refer to the types of conductor core structures used in electrical cables, specifically:
- RE (solid round conductor)
- SE (solid sector conductor)
- SM (stranded sector conductor)
Some products from HELUKABEL include: NAYY (32301), NA2XY (33113), NAYCWY (36009).
5.2 RM 6-30 KV aluminum cables
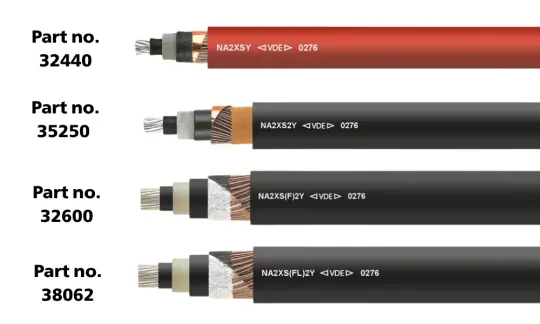
Cables | Structure | Properties, applications | Part number |
NA2XSY | XLPE insulation PVC outer sheath, red color | Used for power distribution stations, indoor installations, and in conduit systems; suitable for outdoor use when protected, underground, and wet environments. It can also be installed on cable trays in industrial plants, switchboards, and substations. | 32440 |
NA2XS2Y | XLPE insulation PE outer sheath, black color | 32520 | |
NA2XS(F)2Y | XLPE insulation PE outer sheath, black color | 32600 | |
NA2XS(FL)2Y | XLPE insulation PE outer sheath, black color | The aluminum/PE protective sheath offers cross water-blocking capability, preventing water ingress and its spread along the cable. In case the sheath is damaged, the impact of moisture is confined to the fault location. The cable is also designed to withstand high mechanical stress during installation and operation. | 38062 |
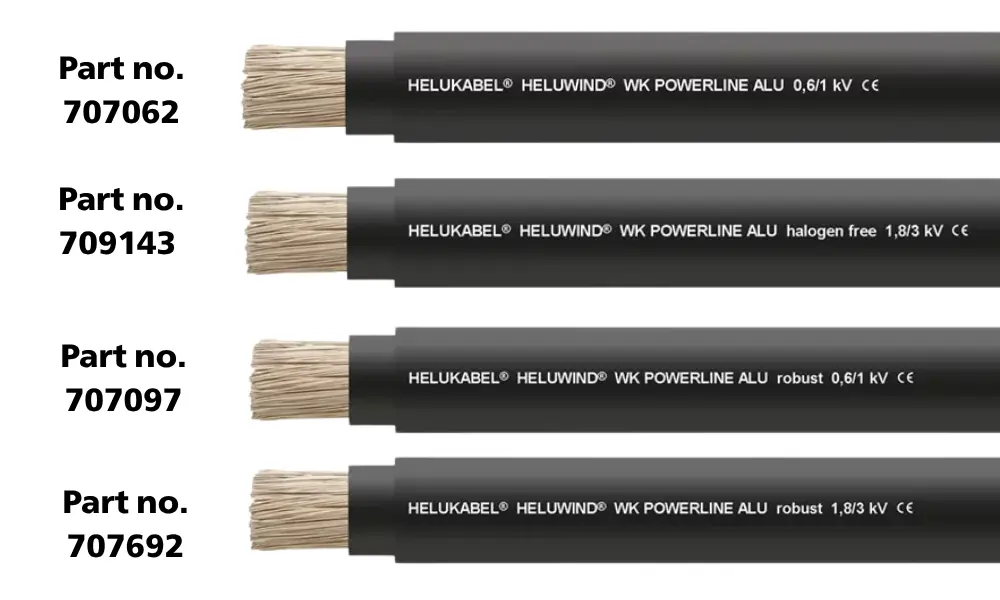
5.3 HELUWIND® WK POWERLINE ALU aluminum cables
HELUWIND® WK POWERLINE ALU is a flexible aluminum power cable featuring a fine-stranded conductor structure, specifically designed for industrial electrical engineering applications - particularly for power cable systems in wind power plants.
With a much lighter weight compared to flexible copper cables and excellent bendability, this cable offers significant advantages in systems where space-saving and reduced mechanical load are critical.
One of its standout features is the ability to be installed in continuous lengths, allowing the cable to be routed throughout the entire wind turbine tower without the need for segmentation by tower levels - greatly shortening installation time.
This cable line is available in various versions, including:
- Versions rated at 0.6/1kV and 1.8/3kV
- Halogen-free options that are environmentally friendly
- “Robust” variants with a special PUR outer sheath that provides high abrasion resistance and mechanical strength
>>See more: Features of cables for wind applications
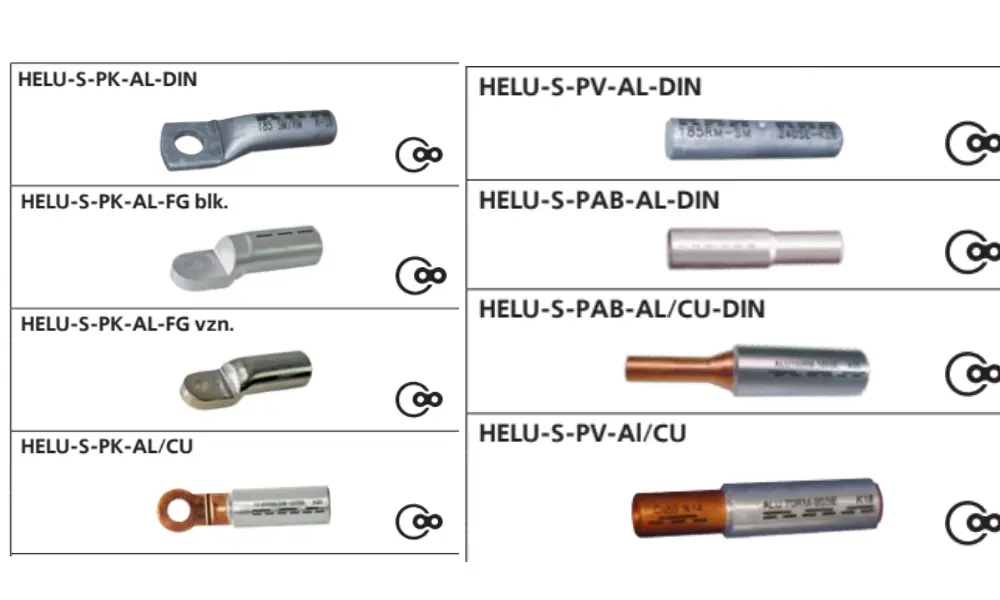
5.4 Aluminum connecting technology and accessories from HELUKABEL
HELUKABEL offers a range of aluminum-compatible connection solutions and cable accessories, including:
- Cable lug: HELU-S-PK-AL-DIN (907865), HELU-S-PK-AL/CU (907568), HELU-S-PV-AL-DIN (907835)…
- Cable fitting
- Cable tool: WK-APW 18 Hydraulic Hand Press, C8-Crimp crimping dies
6. FAQs about aluminum cables
6.1 When should you choose copper or aluminum cables?
Copper remains the most widely used conductor material in electrical systems. Most electrical cables are made from copper due to its excellent electrical conductivity. It is also commonly used in power distribution, power generation, and automotive applications.
However, to reduce weight and cost, utility companies often use aluminum cables for overhead power transmission systems. Aluminum is also preferred in applications where lightweight materials are essential—such as aerospace and next-generation electric vehicles.
In certain cases, such as large coaxial cables, copper-clad aluminum (CCA) is used to combine the high conductivity of copper with the lightweight advantage of aluminum.
6.2 What are CCA cables?
Copper-Clad Aluminum (CCA) cable is a type of conductor with an aluminum core coated with a thin layer of copper (typically around 10%). This design combines the cost-effectiveness and lightweight properties of aluminum with the good electrical conductivity of copper.
CCA is ideal for high-frequency applications (such as RF signals, speaker cables, and antenna cables) where the skin effect causes the current to flow mainly on the surface - the copper layer. Compared to pure copper conductors, CCA is less expensive and lighter, while still offering reliable conductivity when designed and installed according to proper technical standards.
6.3 Can aluminum cables be installed underground?
Aluminum cables can be installed underground when designed for that purpose. Underground cables are specialized types designed for below-ground installation and play a key role in modern power transmission and distribution systems.
Structurally, underground cables typically use copper or aluminum conductors, insulated with high-quality materials such as XLPE or PVC. They may also feature metal armor or shielding layers to protect the conductor from moisture, pressure, and underground temperature variations.
6.4 What should be considered when choosing accessories for aluminum cables?
Not all connectors are compatible with aluminum conductors. Only use connectors that are specifically tested and certified for use with aluminum cables. One critical consideration is galvanic (electrochemical) corrosion, especially when aluminum is in contact with copper. If this issue is not addressed properly, it can lead to corrosion of the aluminum, which may result in overheating or even fire hazards.
To ensure safety and long-term durability, HELUKABEL recommends:
- Using bimetallic terminals (Al/Cu), press connectors, or connecting bolt pins. These accessories are manufactured using friction welding technology, which helps prevent moisture and water ingress.
- Applying additional insulation layers at connection points, such as cold-shrink tubes, hot-shrink tubes, or roll-shrink sleeves.
- Performing regular maintenance of the electrical system
If you still have any concerns or questions, don't hesitate to reach out to HELUKABEL Vietnam's engineering team promptly for detailed assistance.
HELUKABEL® Vietnam
Address | 905, Nguyen Kiem Street, Ward 3, Go Vap District, Ho Chi Minh City 700000, Vietnam |
info@helukabel.com.vn | |
Hotline | +84 28 77755578 |
Website | www.helukabel.com.vn |
Discover our products and place orders | Tiki | Shopee | Lazada | Product finder |
Follow us on | Facebook | LinkedIn | Instagram | Youtube | Zalo | WhatsApp | Tiktok | Spotify |