3 Tips for installing the control cables
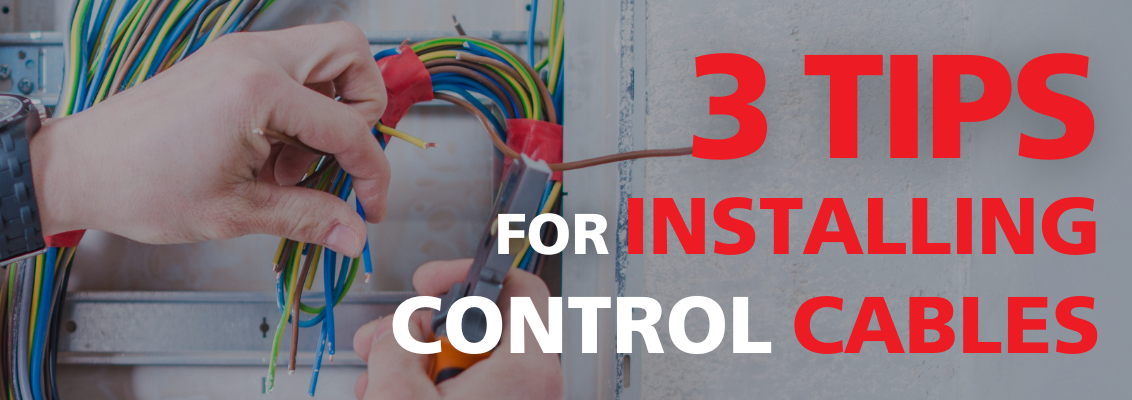
The electrical control system plays an important role in the manufacturing plant. If an error occurs during the construction and installation process, it will affect the life of the conductor, as well as significantly reduce the operating capacity of the plant. Understanding this, our engineers will introduce you to three essential notes when installing control cables, to ensure proper, safe, and effective installation.
1. Basic parameters
When talking about the specifications of control cables, we often hear many terms such as core material, protective shell material, shield tape, voltage, etc. Among them, we need to pay attention to 3 most basic criteria when choosing to install control cables are as follows:
- The conductive core of cables
For the conductive core, you need to know what material the conductive core is made of, how much the core cross-section is, and how the number of small fibers inside the core. From this information, you will be able to consider appropriate construction options to ensure that the transmission efficiency of the cable is not reduced.
The core material and core cross-section will affect the transmission distance. The number of small fibers will increase the softness of the core (increasing the bend radius of the cable) and increase the ability to absorb the vibration caused by the surrounding machinery.
- Shield tape of cables
Shield tape helps control power cables to transmit signals better. They are made of thin aluminum foil or tin-plated copper mesh. The material made of aluminum foil is quite solid, so it is necessary to pay attention to the allowable bend radius to avoid breaking the anti-interference layer of the control cable.
- Voltage of cables
Operating voltage is also a factor you should consider when installing power cables. Normally, cables with a voltage of 300V/500V or 0.6/1kV will be routed to a separate cable tray system from systems with low voltage <100V.
2. The installation environment
Before installing the control cable, you must learn carefully about the technical requirements of the project to have a certain understanding of the operating environment, and the compounds that the power cable must be exposed to every day.
Based on the installation environment, control cables are often classified into many types with features such as anti-interference cables, oil, and chemical-resistant cables, fire-resistant cables, etc.
For example, in the steel manufacturing industry, the power cables selected in the manufacturing plant are often subjected to high temperatures of up to 1000 degrees Celsius, oil resistance, and chemical resistance and some areas also require anti-interference features. Good.
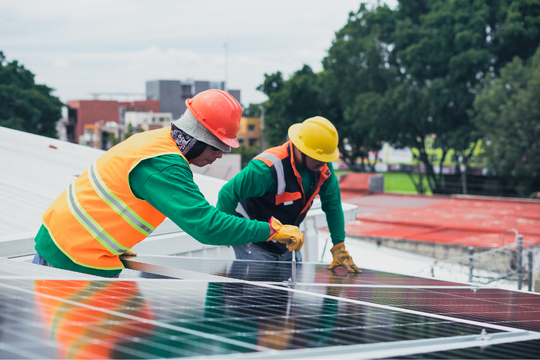
OTHER POSTS >>> CABLE SOLUTIONS FOR THE RC-10 AND RC-RB1 DRILLING RIG
>>See more: Tips for choosing cable in control cabinet
3. The installation procedure
In the process of installing control cables , there are two important factors we need to pay attention to the installation position between the power cables and the ambient temperature of the power cables.
Both of the above factors directly affect the amperage. That affects the electrical transmission process for equipment in the production process.
- Installation position between power cables
For the installation location between cables, the cause of the difference in amperage is due to the heat generated inside the power cable. At that time, electricity will be lost due to the process of converting electrical energy into heat energy.
If the cables are located next to each other, during power transmission, the temperature between the cables will resonate, causing the total temperature to increase, and reducing the amperage in the cable.
For example, at a room temperature of 30°C, we can install cables in two ways.
On face without inter-contact | On surface with inter-contact | |
30°C (factor 1) | 12A | 9A |
60°C (factor 0.82) | 9.84A | 7.38A |
- Ambient temperature of power cable.
Installation ambient temperature has a great influence on the amperage of the cable. A temperature of 30°C is considered ideal for current when the coefficient of change is not too much, but as the temperature rises to 60°C, the amperage will drop significantly. Therefore, in the process of installing control cables, we must carefully consider the installation environment as well as the arrangement of cables so that the cables work with the best efficiency.
With the 3 notes mentioned in the article, hopefully, you have some useful information, which will help in the installation of the factory's electrical cable system. The correct installation of power cables not only saves electricity, ensures the life of the cable, but also helps to ensure safety and limit unwanted incidents.
Please visit our E-STORE on TIKI to find out more many products.