Frequently asked questions about electrical cables
When choosing electrical cables, there are many factors to consider—from structure and materials to characteristics and cable types. This article compiles essential information to help users simplify the cable selection process.
1. Electrical cable basis
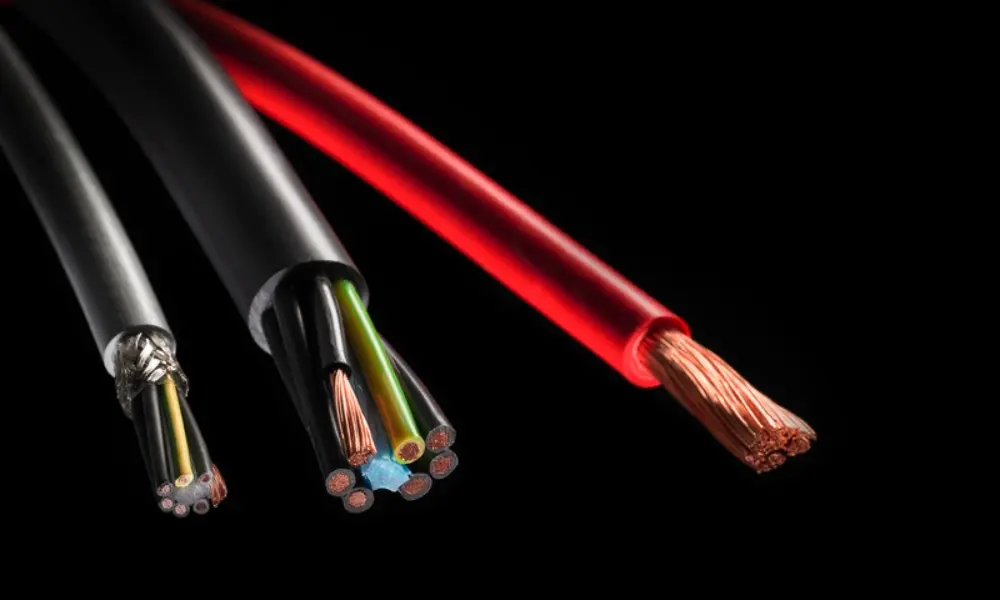
1.1 What are the difference between cables and wires
Although both wires and cables are vital components in electrical systems, they are not the same.
A wire is a single electrical conductor made of copper or aluminum. It can be solid or stranded (multiple twisted strands). Wires may be bare or insulated with color-coded sheaths. Wire sizes are typically measured using the American Wire Gauge (AWG) standard—lower AWG numbers mean thicker wires with higher current-carrying capacity.
A cable, on the other hand, consists of two or more insulated conductors bundled together and covered with an overall protective sheath. Cables usually contain hot (live), neutral, and ground conductors.
>>See more: What are AWG and AWG cables?
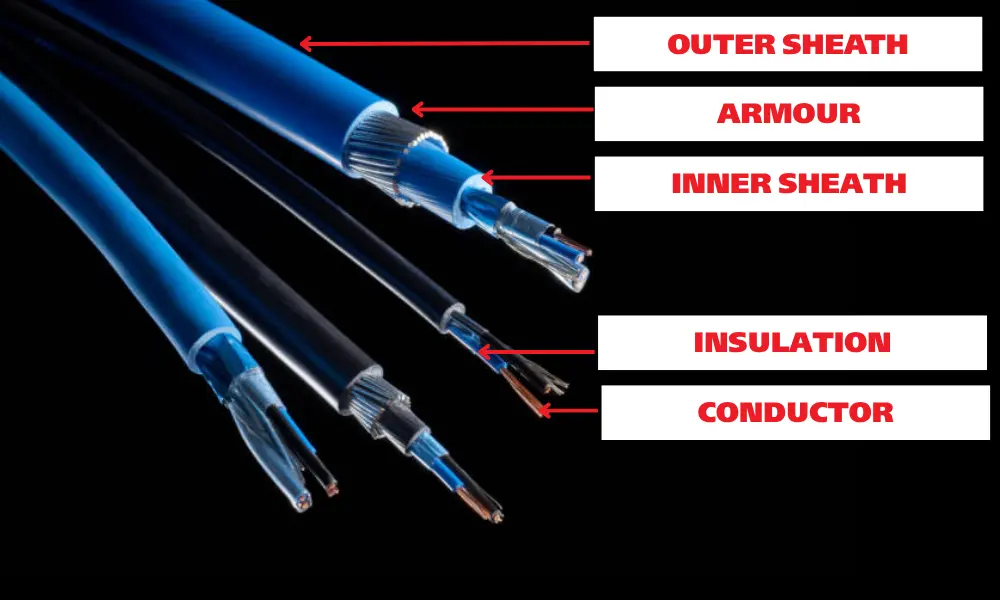
1.2 What are the components of an electrical cable?
A standard electrical cable typically includes:
- Conductor: The core component responsible for carrying current. It must have sufficient cross-sectional area to avoid overheating.
- Insulation: Surrounds the conductor, providing electrical resistance and thermal stability.
- Outer sheath: Protects against moisture, weather, chemicals, and mechanical damage.
Additional layers may include shielding (to prevent EMI) and armor for mechanical protection.
>>Find out more: Features, components, and applications of electrical cables
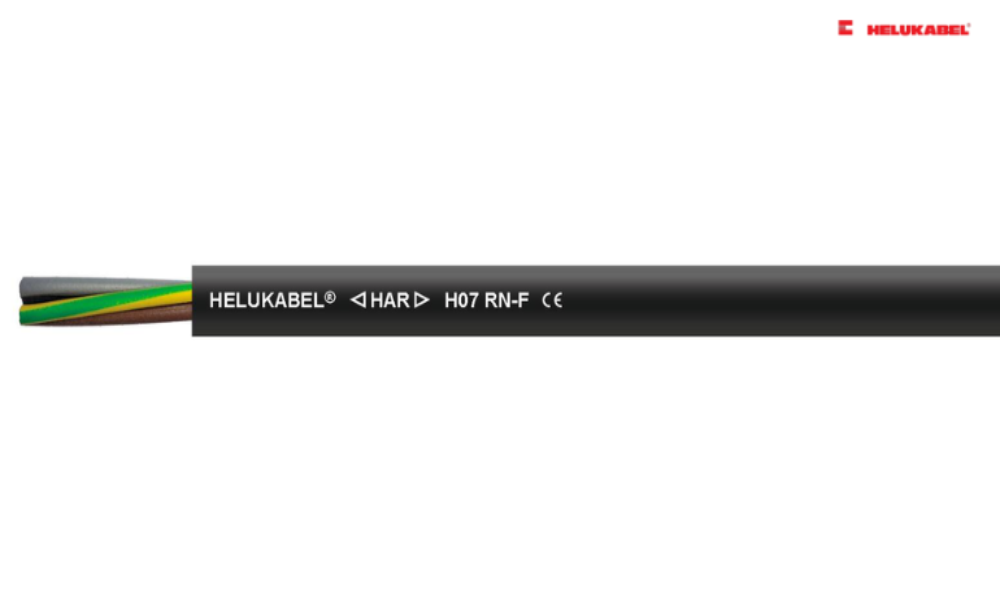
1.3 What do the letters and numbers printed on electrical cables mean?
Cable markings are standardized abbreviations used to convey essential information about a cable’s technical specifications and areas of application. These markings may include the cable type, rated voltage, insulation and sheath materials, conductor cross-sectional area, and the number of cores.
Standardizing these designations ensures that users can accurately identify the cable’s specifications regardless of the manufacturer. This is particularly important for selecting and installing cables that meet safety and performance requirements in electrical systems.
Let’s take an example: H07RN-F 3G1.5 Each segment of this code has a specific technical meaning:
- H: Indicates this is a harmonized cable, manufactured in accordance with European standards.
- 07: Specifies a rated voltage of 450/750V.
- R: Denotes that the core insulation is made from ethylene-propylene rubber (EPR).
- N: Indicates the outer sheath is made from polychloroprene rubber (CR).
- F: Signifies a flexible cable made of fine stranded conductors, suitable for applications requiring high flexibility.
- 3: Represents the number of cores in the cable.
- G: Stands for “Ground,” indicating the presence of a green-yellow protective earth conductor.
- 1.5: Specifies that each conductor has a cross-sectional area of 1.5 mm².
2. Electrical cable conductors
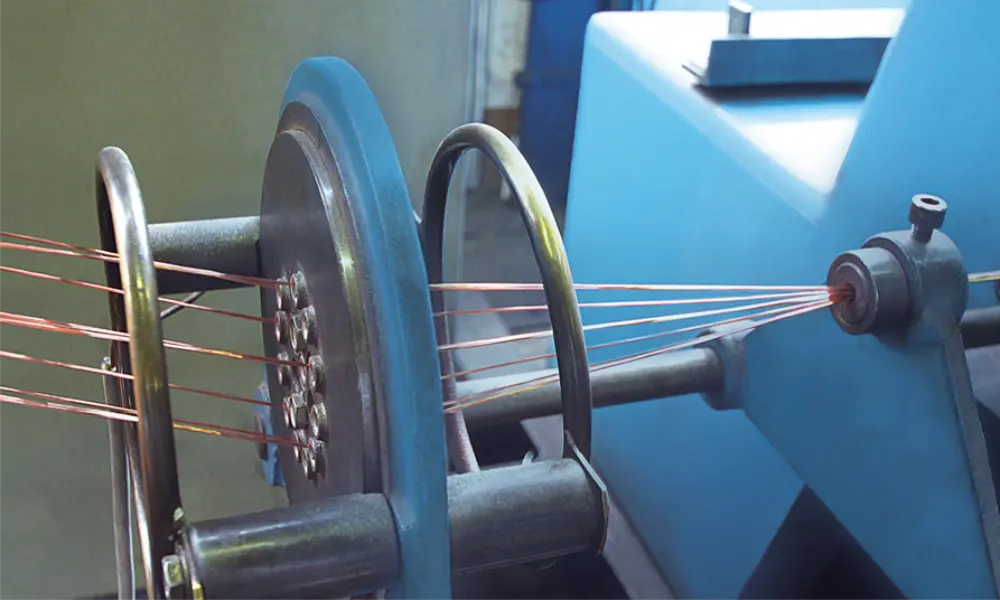
2.1 What are the differences between solid wire and stranded wire?
Solid wire consists of a single, continuous metal core, whereas stranded wire is made up of multiple small strands twisted together to form a single conductor.
Stranded wire is composed of many thin wire strands compressed together and covered with an insulating, non-conductive sheath. Thanks to its flexibility and bendability, stranded wire is ideal for applications where frequent bending or complex routing is required — such as in printed circuit boards (PCBs) or in compact spaces.
In contrast, solid wire tends to be thicker and heavier. It is preferred for outdoor or fixed installations that demand high current capacity and long-term mechanical strength.
2.2 Stranding types
There are several types of stranding configurations, each with unique characteristics:
Stranding type | Features |
Concentric strand | Features a central core wire surrounded by one or more layers of helically twisted wires. Each successive layer contains six more strands than the previous one. |
Bunch strand | Consists of small wire strands twisted in the same direction without a specific geometric arrangement. |
Rope strand | A type of concentric strand where each component strand is itself a small bunch of twisted wires. |
Sector conductor | A conductor with a cross-section resembling a sector of a circle (fan-shaped). |
Segmental conductor | A round conductor composed of 3 or 4 lightly insulated sector-shaped segments. |
Annular conductor | A round conductor with a hollow center, made by spirally wrapping wires around a non-conductive core. |
Compact strand | A round or sector-shaped conductor with all layers twisted in the same direction and compressed into a predefined compact shape. |
Compressed strand | Similar to compact strands, these are also round or sector-shaped conductors where all layers are twisted in the same direction and then mechanically compressed to form a uniform shape. |
2.3 What is the significance of conductor class classifications in electrical cables?
Electrical cable conductors are classified into four main classes based on their construction and flexibility:
- Class 1 and Class 2 are designed for use in fixed installation cables.
- Class 5 and Class 6 are designed for flexible cables but can also be used in fixed installations if needed.
Classification breakdown:
- Class 1: Solid conductor
- Class 2: Stranded conductor
- Class 5: Flexible conductor – made of finer strands, offering better flexibility.
- Class 6: Extra-flexible conductor – even more finely stranded than Class 5, offering the highest level of flexibility among all classes.
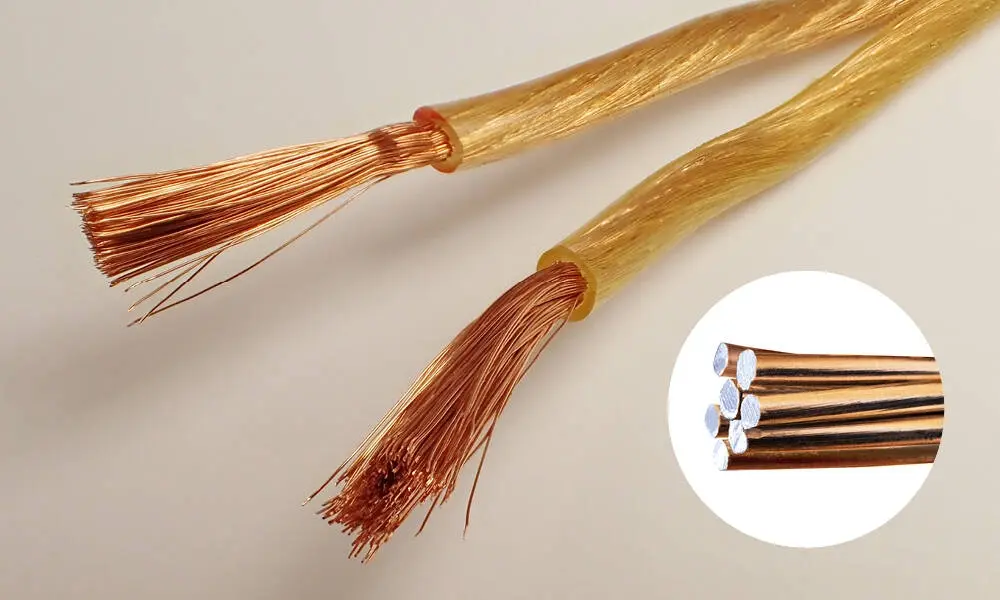
2.4 When should copper conductor cables be used, and when are aluminum conductor cables more suitable?
Thanks to its superior conductivity, copper is the primary material used in most electrical cables, as well as many electrical devices and components. Copper conductors are widely used in power transmission, power generation, and the automotive industry due to their excellent electrical performance.
However, aluminum is often preferred in overhead transmission lines by utility companies because it is more cost-effective and lighter than copper. These characteristics also make aluminum cables highly favored in industries where weight reduction is critical, such as aerospace and next-generation electric vehicles.
In some specialized applications - such as large-diameter coaxial cables, copper-clad aluminum (CCA) conductors are used. This material combines the high conductivity of copper with the light weight of aluminum, offering a balanced performance at lower cost and mass.
2.5 What is the difference between single-core and multi-core electrical cables?
A single-core cable (or single-conductor cable) contains only one conductive core surrounded by an insulating layer.
A multi-core cable (or multi-conductor cable) consists of multiple insulated conductors, each individually insulated and grouped together under a common outer sheath.
3. Insulation and sheathing in electrical cables
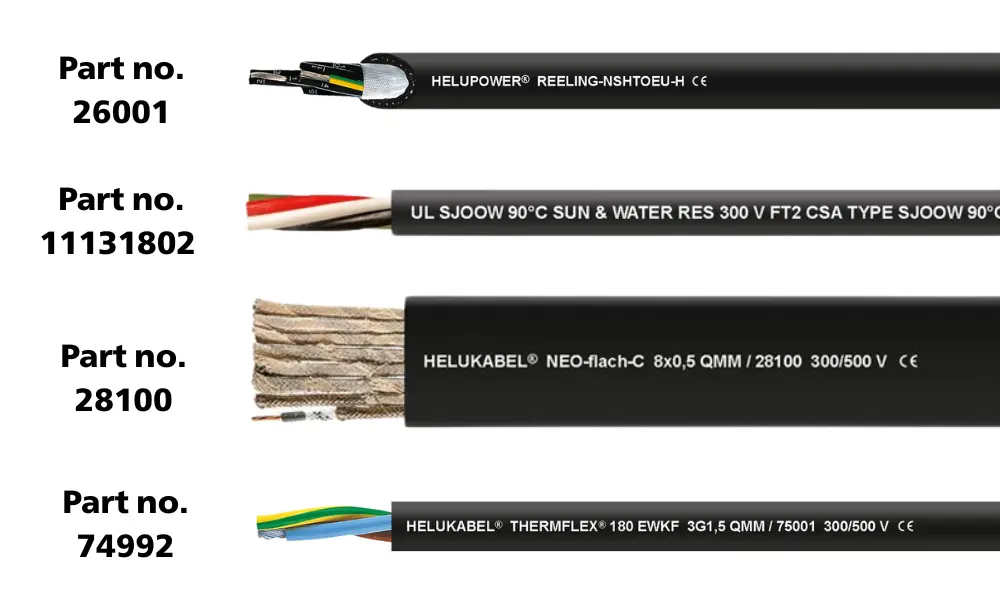
Rubber-insulated cables from HELUKABEL
3.1 What materials are used for insulation and sheathing in electrical cables?
The most commonly used materials for cable insulation and sheathing are thermoplastics and thermosets.
- Thermoplastic materials can be softened when heated and molded into desired shapes. Once cooled, they retain their new shape. A key characteristic of thermoplastics is that they can be melted and reshaped multiple times without altering their fundamental structure.
- Thermosetting materials, on the other hand, can also be softened and shaped with heat—but only once. This is because during the shaping process, they undergo a chemical cross-linking reaction (polymerization), which makes them unable to melt again after setting.
Group | Material type | Features |
Thermoplastic | PVC | A widely used, cost-effective, and flexible material, suitable for many general applications. |
Fluoropolymers | Used for low-voltage insulation, includes types like Teflon (PTFE, FEP, PFA), Tefzel (ETFE), Halar (ECTFE), and Kynar or Solef (PVDF). | |
Polyethylene (PE) | Excellent electrical properties with low dielectric constant and very high insulation resistance. | |
Polypropylene (PP) | Shares similar electrical properties to PE, but offers higher rigidity. | |
Thermoplastic Elastomer (TPE) | Exceptional cold resistance, ideal for insulation and sheath applications in cold climates. | |
Polyurethane (PUR) | Mainly used as a cable sheath due to its outstanding abrasion resistance. | |
Thermosetting | Neoprene (CP) | Produces highly elastic sheaths that resist permanent deformation under heat and stress; also remains flexible at low temperatures. |
Cross-linked Polyethylene (XLP or XLPE) | Commonly used for insulation in household wiring (600V), and for medium- and high-voltage power cables (5 kV to 69 kV+), as well as in control cables. | |
Ethylene Propylene Rubber (EP, EPR, or EPDM) | A widely used synthetic rubber for cable insulation due to its thermal and electrical properties. | |
Silicone | A soft, rubber-like insulating material with a wide operating temperature range from –80°C to 200°C. |
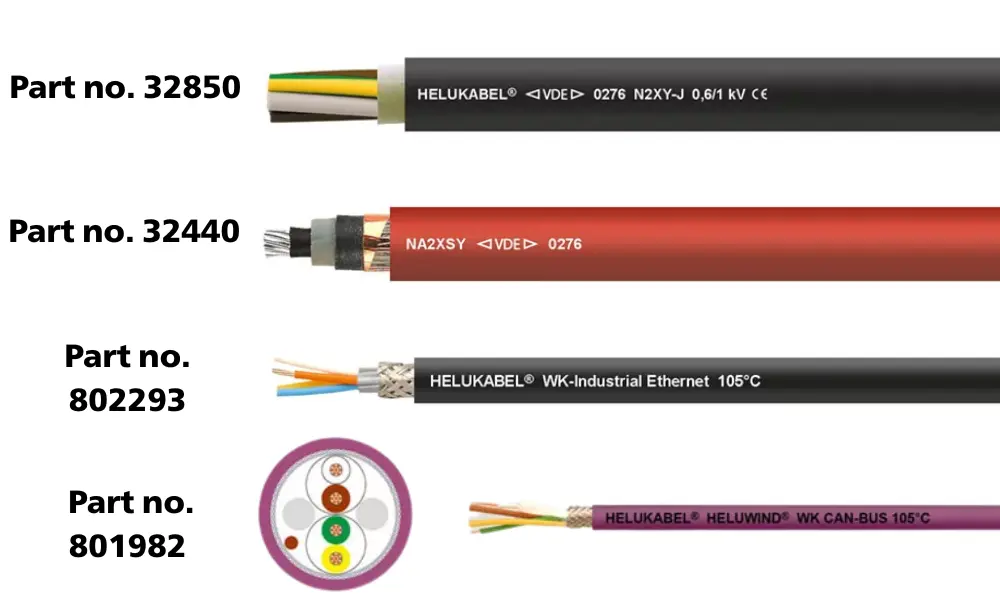
XLPE-insulated cables from HELUKABEL
3.2 When should XLPE-insulated cables be used?
PVC is the most commonly used material for cable insulation and sheathing due to its low cost and stable performance in most residential and general applications. However, in certain conditions, XLPE (Cross-linked Polyethylene) becomes the superior choice.
XLPE offers a higher maximum operating temperature—up to 90°C. This means that, when comparing XLPE-insulated cables and PVC-insulated cables of the same conductor size, XLPE cables can carry a higher current load.
Moreover, for the same current-carrying requirement, XLPE cables may allow the use of a smaller conductor cross-section than PVC cables—without compromising performance. This can help optimize the design and cost-efficiency of the electrical system.
The cross-linking process in XLPE enhances resistance to oil, chemicals, and thermal degradation, even at elevated temperatures. Thanks to these advantages, XLPE is commonly used in fire-resistant cables or LSZH (Low Smoke Zero Halogen) cables, where both electrical performance and safety are critical.
>>See more: A glance at XLPE material and XLPE-insulated cables
4. Shielding and armor
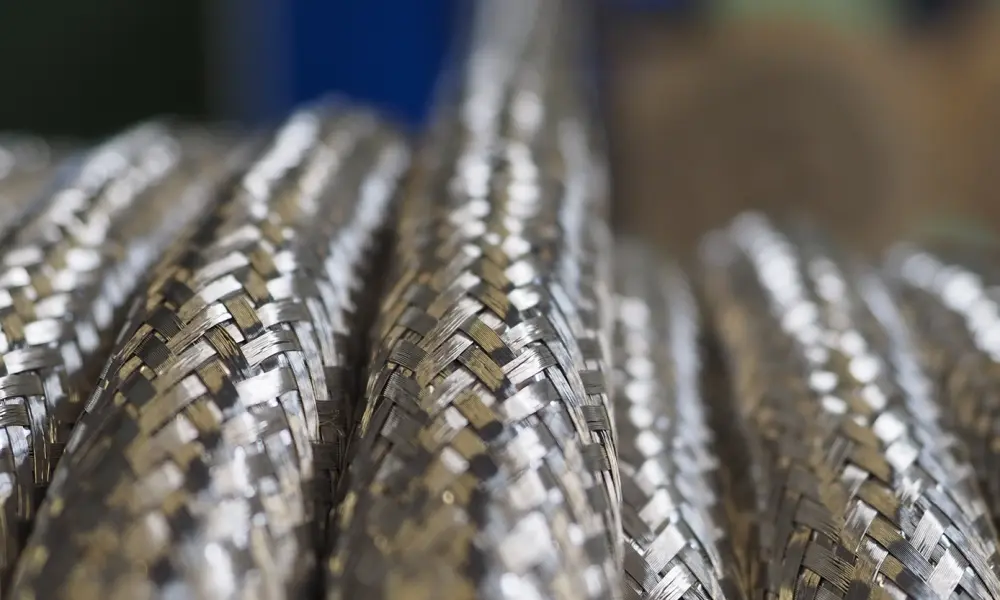
A braided C screen cable with tinned copper mesh provides coverage exceeding 85 per cent
4.1 What is cable shielding?
Shielding (also known as a screen) is a metallic layer wrapped around an insulated conductor or group of conductors. While the structure may look similar in different cable types, the function of shielding varies depending on the application.
- In signal and electronic cables, shielding is primarily used to block electromagnetic interference (EMI) and prevent signal distortion.
- In power cables, shielding primarily protects users from electrical shock and helps prevent partial discharges (corona effect), thereby increasing cable reliability and safety.
Common types of cable shielding include foil shield, braided shield, spiral shield.
4.2 What is the role of cable armor?
In many installations, electrical cables are exposed to harsh mechanical stresses such as crushing, impacts, or pulling forces. If not properly protected, these forces can damage the insulated conductors or fiber optics inside the cable.
To address this, cables are often equipped with an armor layer—typically made of metal—wrapped over the cable core. This armor provides mechanical protection against external physical damage, extended cable lifespan, enhanced safety, and improved operational reliability in demanding environments.
5. Common types of electrical cables: Key differences
5.1 What are the differences between power cables and control cables?
Power cables are primarily used for transmitting electrical energy from one point to another. These cables are designed to carry high current loads and are used to supply power to equipment, machinery, and electrical systems that require stable energy input to operate.
In contrast, control cables are not meant for power transmission. Instead, they are used to transmit control signals. These cables are responsible for connecting control devices such as switches, push buttons, sensors, and other components to control systems. Their main purpose is to regulate and coordinate the operation of machines, equipment, or manufacturing processes.
>>See more: Control and signal cables from HELUKABEL
5.2 What are the differences between signal cables and control cables?
Signal cables are specifically designed to transmit sensitive signals, often in low-voltage and low-current applications. They play a critical role in a wide range of systems - from transmitting data from sensors and measurement devices to enabling data communication via the internet or industrial networks. Signal cables often require high accuracy and stability in signal transmission and are usually built with EMI shielding to protect against signal distortion.
By contrast, control cables are used to carry control signals or low-voltage power to and from electrical control devices. While they may transmit signals like signal cables, they are also capable of carrying higher voltage and current, especially in industrial automation systems where durability and electrical performance are key. As a result, control cables are more robust and are engineered to handle electromechanical loads better than signal cables.
5.3 What are the differences between twisted pair cables and coaxial cables?
Twisted pair cable consists of two insulated copper conductors twisted together. This twisting helps reduce EMI from external sources and also minimizes crosstalk between neighboring cables. Twisted pair cables are commonly used in computer networking (LAN) and telephone lines.
Coaxial cable, on the other hand, features a single central conductor surrounded by an insulating layer, which is then wrapped in a metal shield (usually braided copper or aluminum foil) to protect against signal interference. Coaxial cables are widely used in cable television systems, CCTV security cameras, and high-speed internet connections.
5.4 Are LAN cables, Ethernet cables, and Network cables the same?
LAN cable (Local Area Network cable ) refers to any cable used to connect devices within a localized area—such as homes, schools, or office buildings. These cables usually utilize twisted pair wiring to transmit electrical signals over short distances.
Ethernet cable is a specific type of LAN cable that conforms to Ethernet networking standards (e.g., IEEE 802.3). It’s designed to connect devices like PCs, routers, switches, and modems within a wired network. Ethernet cables are categorized (Cat5e, Cat6, Cat6a, etc.) based on their speed, bandwidth, and shielding.
Network cable is a broad, generic term that includes all types of cables used for data transmission within a computer network. This includes: Ethernet cables, fibre optic cables, coaxial cables.
5.5 What are the differences between temperature-resistant, fire-resistant, and flame-retardant cables?
Temperature-resistant cables are designed to withstand high temperatures without melting or degrading in performance, but they are not meant to resist direct flame or fire exposure. It is important not to confuse temperature resistance with fire resistance - a cable can tolerate high temperatures yet still ignite easily, whereas a fire-resistant cable may only function within a certain temperature range and time limit during a fire.
Fire-resistant cables , are engineered to continue functioning during fire conditions. These cables are crucial for emergency systems such as fire alarms, smoke control, emergency lighting, and fire-fighting equipment, where maintaining power or signal transmission is essential during a fire event.
Flame-retardant cables are designed to slow down or prevent the spread of flames along the cable surface. While they help contain the fire, they are not capable of maintaining electrical functionality during fire exposure.
5.6 Differences between CV, CVV, CXV cables
CV, CVV, and CXV cables are all types of power cables with copper conductors, commonly used in electrical installations. Their main differences lie in the insulation and sheath materials, which affect their flexibility, temperature rating, and current-carrying capacity.
- CV cables (Cu/PVC): copper conductor, PVC insulation, no outer sheath
- CVV cables (Cu/PVC/PVC): copper conductor, PVC insulation, PVC outer sheath
- CXV cables (Cu/XLPE/PVC): copper conductor, XLPE insulation, PVC outer sheath
If you still have any concerns or questions, don't hesitate to reach out to HELUKABEL Vietnam's engineering team promptly for detailed assistance.
HELUKABEL® Vietnam
Address | 905, Nguyen Kiem Street, Ward 3, Go Vap District, Ho Chi Minh City 700000, Vietnam |
info@helukabel.com.vn | |
Hotline | +84 28 77755578 |
Website | www.helukabel.com.vn |
Discover our products and place orders | Tiki | Shopee | Lazada | Product finder |
Follow us on | Facebook | LinkedIn | Instagram | Youtube | Zalo | WhatsApp | Tiktok | Spotify |