How to identify the quality of industrial control cables?
Choosing the right control cables for specific applications is necessary, but the greater emphasis should also be placed on how to select quality cables.
Control cables are used to transmit signals and control mechanical equipment. Choosing high-quality control cables not only directly affects the operation process but also affects the performance of equipment, machinery, and the safety of the electrical system.
>>Find out more: Common types of electric cables
1. Risks of using inferior control cables
1.1 Electric short-circuit and fire
Poor quality control cables often do not meet electrical safety standards, easily causing problems such as short circuits and fires. These incidents can endanger workers and cause damage to equipment, causing losses to the business. In addition, these cables are often not technically guaranteed. Therefore, using these cables in harsh conditions such as high temperatures, chemical environments, oily environments... also poses additional risks.
1.2 Reduced performance
Low-quality cables may lack the necessary design to handle the required current, resulting in decreased efficiency within the electrical system. Consequently, power cables may break or sustain damage, diminishing productivity and causing operational delays. Other issues that may arise include power loss, unstable machinery operation, and a shortened lifespan for the electrical system.
1.3 Technically incompatibility
Control cables play an important role in signal transmission. Therefore, control cables that are not compatible can cause this process to be interrupted and the signal to flicker and be unstable. In environments prone to electromagnetic interference, such as manufacturing or mechanical plants, the lack of reliable anti-interference control cables or the presence of substandard ones can lead to considerable losses.
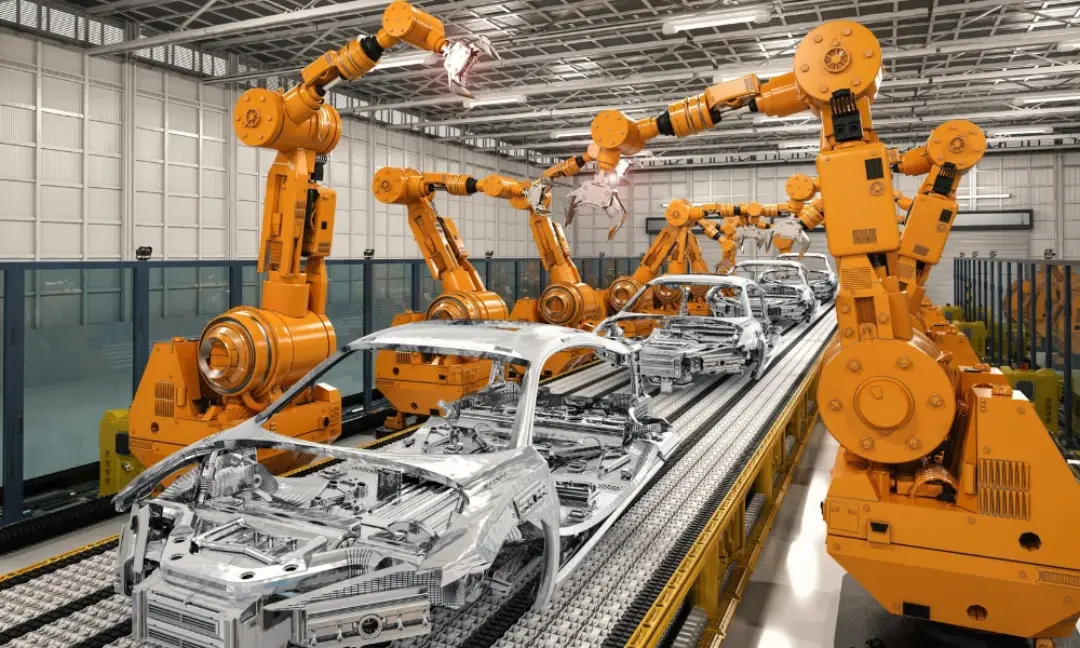
2. How to identify the quality of control cables?
To check the quality of the control cable, users can perform the following methods:
2.1 Visual assessment
Visual assessment is the first step in evaluating the quality of control cables. When checking cables, the following factors should be taken into consideration:
Inspecting the appearance of the control cable
High-quality cables usually have a smooth appearance, without peeling or cracking. If the cable shows signs of not meeting specifications or has material issues, it may be a sign of a poor-quality cable.
In addition, the symbols printed on standard control cables often contain important information such as manufacturer, technical standards, specifications... This piece of information helps users somewhat identify whether the cable meets safety and quality standards.
Inspecting the quality of the conductors
To assess the quality of conductors, users can rely on the following factors:
- Color: High-quality copper cores typically exhibit a purple-red hue, appearing shiny and uniform. In contrast, inferior or counterfeit copper cores often appear purple-black and may display a yellow or white tint due to impurities.
- Touch: Superior copper cores impart a sense of softness and flexibility when touched. Conversely, poor-quality copper cores feel solid, stiff, and inflexible.
- Toughness and mechanical strength: High-quality copper cores usually have good toughness and mechanical strength. Meanwhile, poor quality copper cores often have a low level of flexibility and break easily when bent or stretched.
- Impurities and uniformity: High-quality copper cores tend to have fewer impurities and a more uniform structure compared to inferior cables.
- Response to magnets: High-quality copper cores do not react to magnets. Meanwhile, counterfeit copper core can often be attracted to the magnet because it contains many impurities and is structurally uneven.

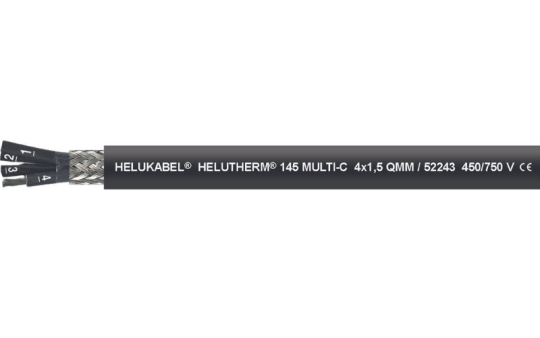
Insulating sheath assessment
Users need to check the insulation sheath surrounding the wire. It should not have cuts, scratches, or any signs of damage. High-quality insulation ensures proper insulation and protection against electrical faults. The insulating sheath of high-quality cables is often made from high-quality insulating materials, such as PVC or XLPE, ensuring mechanical durability and certain flexibility. This material does not tear easily and retains its insulating properties for a long time. In some cases, the insulating sheath can be made of natural rubber, meeting the requirements for insulation and durability.
>>Find out more: How important are shield and armour?
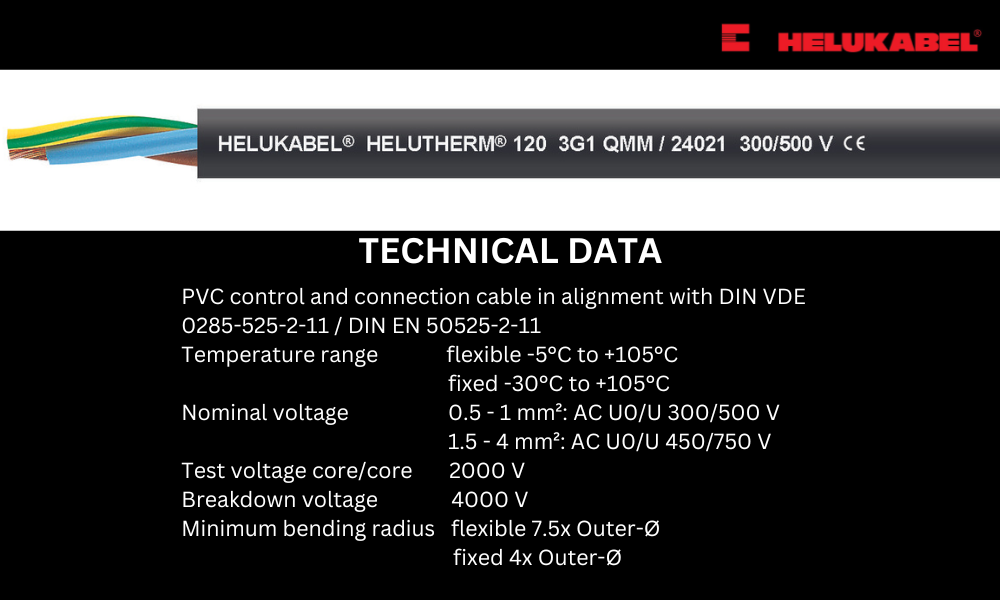
Data sheet of HELUTHERM® 120 control cable
2.2 Data sheet-based assessment
Evaluating the quality of control cables through examination of the datasheet (technical specifications) ensures users select products that align with their requirements. The datasheet offers crucial information including:
- Material type: Data sheets often provide information about the type of material used for the insulating sheath and conductor. For example, control cables with PVC or XLPE insulating sheath often have high durability and good insulation.
- Flexibility: This parameter indicates the flexibility and hardness of the cable, important to determine the product's ability to bend and install in the working environment.
- Heat resistance: This property is important in environments with high temperatures or temperature fluctuations. The data sheets will indicate the maximum temperature the cable can withstand without affecting performance.
- Standards: Data sheets commonly detail the quality standards to which the cable has been subjected and adheres to, ensuring compliance and reliability.
2.3 Assessing the quality of control cables based on actual tests
Assessing the quality of control cables through actual testing involves employing specialized equipment, although some initial assessments can be conducted using simple tools.
Continuity check
A multimeter can be used to test the continuity of the conductive core inside the control cable. This helps to ensure that there are no open circuits or short circuits that could cause power interruption or electrical hazards.
Insulating resistance check
This test measures the resistance between the conductor and the insulation. Higher insulating resistance indicates better quality. An insulation resistance tester, commonly known as a megger, is used for this purpose.
Voltage drop check
Voltage drop measurement assesses the cable's performance under specific currents. Excessive voltage drops can result in power loss and inefficient operation of connected devices. However, it's important to note that the voltage drop varies based on the cable's length and current capacity.
3. How to choose appropriate control cables?
In addition to considering the quality of the control cable, users must take several factors into account to ensure that the selected cable is both of high quality and compatible with their needs.
3.1 Determining the number of cores of the control cable
The number of cores directly impacts the cable's capacity to transmit signals and data. Each core can accommodate one or multiple different signals, and the appropriate number of cores depends on the quantity of signals that need to be transmitted within the control system.
For instance, 2-core control cables are suitable for simple control devices with minimal sensors, while 4-core cables are more suitable for systems equipped with numerous control devices and sensors. In more complex control systems, 8-core cables are often preferred.
>>See more: HELUKABEL's different types of control cables
3.2 Determining the transmission distance
Transmission distance refers to the maximum distance an electrical signal can be transmitted over an electrical cable without experiencing significant loss. For control systems, ensuring the signal reaches its destination reliably is very important.
As per the Inverse Square Law, any increase in distance from the source results in a proportional decrease in signal strength inversely proportional to the square of the distance increase. In practical terms, this implies that doubling the distance equates to quartering the signal strength, while tripling the distance reduces signal strength to one-ninth.
Therefore, when long-distance transmission is needed, users should opt for anti-interference control cables to mitigate signal loss during transmission.
>>Find out more: Top 3 tips for installing control cables
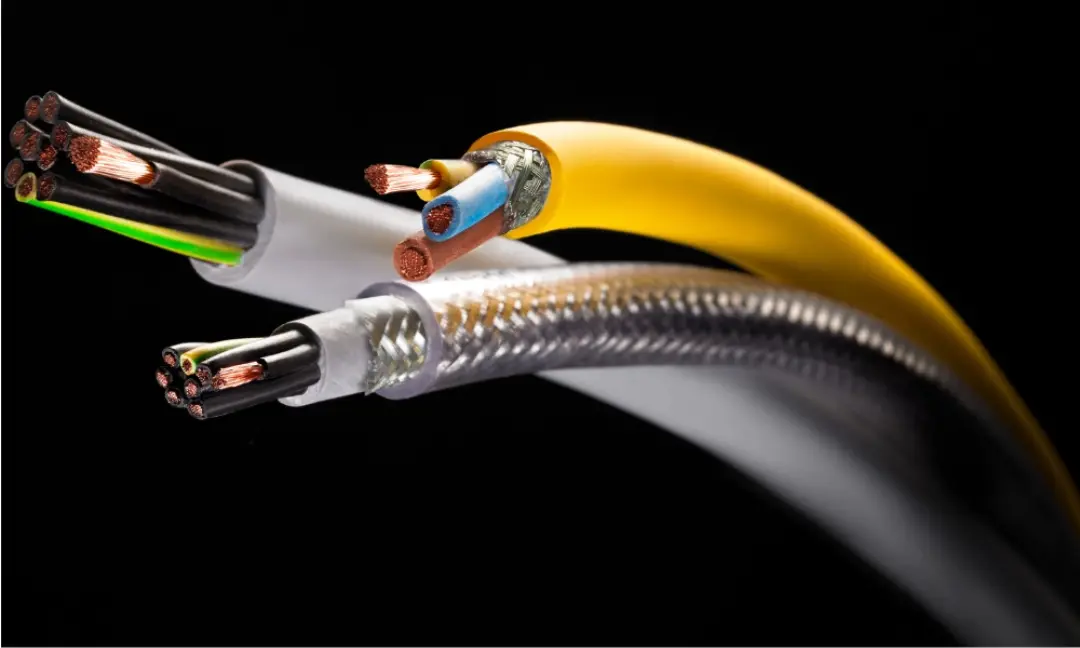
3.3 Considering environmental conditions
For each specific environment, users need to pay attention to the types of specialized control cables to help the power cables operate normally and stably. Besides, the operating environment of electric cables also directly affects the choice of cable material.
- Fire-resistant control cables: usually have an outer protective layer to increase durability, is able to withstand high temperatures and does not emit toxic smoke when burning. This outer sheath can be made from PVC, LSZH or other fireproof materials.
- Anti-interference control cables: help minimize the effects of electromagnetic interference (EMI) and interference from external noise sources. This is extremely important in environments with many electronic devices or exposure to noise sources.
- Oil-resistant control cables: constructed with oil-resistant materials, serve to mitigate damage and abrasion incurred from exposure to oil and other petrochemicals. This attribute proves indispensable in industrial settings like factories, manufacturing facilities, or areas where contact with oils and fluids is prevalent.
>>See more: 3 types of cables in oil environments