Insulation resistance and 3 influential factors to its value
Industrial electrical safety is always a top priority. To mitigate operational issues, machine users should pay attention to insulation resistance.
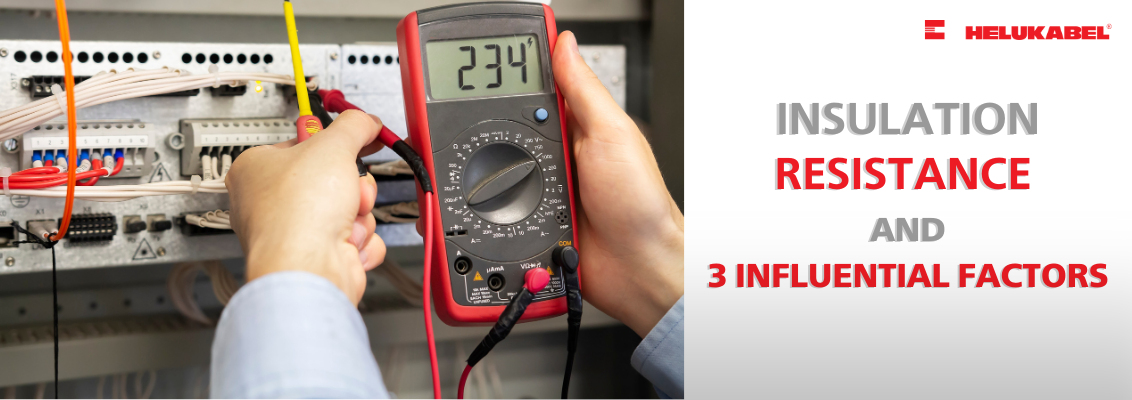
What is insulation resistance?
Insulation resistance is the measurement value of the electrical resistance of insulating materials. An insulating material has a specific resistance value which represents the insulating ability of the device being measured. The higher the measured insulation resistance, the better the device's insulation ability and vice versa.
Basically, insulation resistance is a parameter that lets us know the insulation ability of a device. Also, it helps maintenance engineers quickly detect abnormalities in machines to repair and limit dangerous electrical leaks.
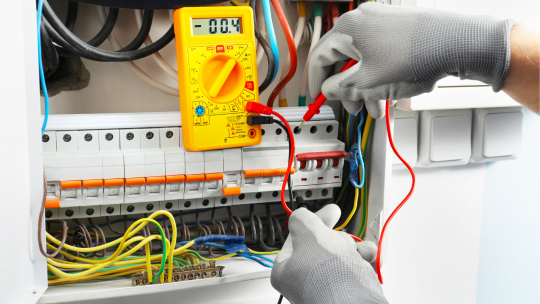
3 factors that affect insulation resistance
In addition to checking the connecting wires, the device's shell and the power cable, it is necessary to pay attention to the following three factors to ensure the insulation resistance of the device is always at the best level:
Factor 1: Temperature
Unlike the resistance of the conductor, the insulation resistance decreases as the temperature of the device increases. The reason comes from the very low density of electrons in the insulator, making the mobility of electrons here higher than in conductors. This makes it easier for electrons to move as the temperature increases and reduces the resistance of the insulator, specifically the cable's shell.
Different materials have distinctive insulation resistance with temperature, and it is difficult for maintenance staff to ensure that measurements are taken exactly at the same temperature. Therefore, when insulation resistance is measured, the test temperature (including ambient temperature and device temperature) must be recorded. Please note that the measurements must be performed at a temperature range as close as possible to each other to avoid errors due to temperature conversion.
Factor 2: Moisture and dirt on the device surface
On rainy days with high humidity, water vapor can easily condense on the surface of devices and electric cables. If this problem lasts for a long time, the wire surface will be covered with a layer of steam, which reduces the insulation resistance value of the wire or device.
In addition, when machines and devices operate for a long time in a manufacturing plant, it is easy for dirt and oil to accumulate on the surface. These two factors combined will reduce the ability of the insulation layer on the device and conductor to impede the flow of electricity.
To overcome this situation, you need to observe the fan system in factories, ensure the air is always dry and cool, and regularly clean machines. Simultaneously, you should choose a suitable cable for the factory environment. In particular, the cable should have an insulating sheath that is resistant to oil and chemicals. Also, do not forget to make certain that the quality of the insulating sheath is not affected too much by environmental factors.
Factor 3: Residual charge
Residual charge is the charge left over during the operation of the device. This will make the value of the insulation resistance change uncontrollably, causing the measured insulation impedance to be inaccurate.
In addition, if the amount of residual charge is too large, it can endanger the person using the device. To eliminate the effects of residual charge, make sure to fully discharge the charge through the earthing wire before measuring the insulation impedance.
Please contact us at:
HELUKABEL® Vietnam
905, Nguyen Kiem Street, Ward 3, Go Vap District, Ho Chi Minh City 700000, Vietnam
Tel. +84 28 22536441 | info@helukabel.com.vn | www.helukabel.com.vn
SCHEDULE A MEETING WITH OUR ENGINEERS HERE !